A Comprehensive Overview to the Refine and Advantages of Plastic Extrusion
In the huge realm of manufacturing, plastic extrusion arises as a necessary and highly effective process. Transmuting raw plastic into constant accounts, it caters to a myriad of markets with its exceptional adaptability.
Comprehending the Basics of Plastic Extrusion
While it might appear complex in the beginning look, the process of plastic extrusion is essentially straightforward - plastic extrusion. It is a high-volume manufacturing method in which raw plastic is melted and formed right into a continuous profile. The procedure starts with the feeding of plastic product, in the kind of granules, powders, or pellets, right into a heated barrel. The plastic is after that melted using a mix of warm and shear, used by a rotating screw. As soon as the molten plastic gets to the end of the barrel, it is compelled through a small opening recognized as a die, shaping it into a wanted kind. The shaped plastic is then cooled, strengthened, and cut into desired sizes, completing the procedure.
The Technical Refine of Plastic Extrusion Explained

Kinds Of Plastic Suitable for Extrusion
The selection of the best kind of plastic is an important element of the extrusion process. Different plastics use unique homes, making them extra matched to specific applications. Polyethylene, for instance, is frequently utilized because of its reduced price and simple formability. It supplies superb resistance to chemicals and dampness, making it suitable for products like tubing and containers. In a similar way, polypropylene is an additional popular choice because of its high melting factor and resistance to exhaustion. For even more robust applications, polystyrene and PVC (polyvinyl chloride) are typically selected for their toughness and resilience. These are common alternatives, the choice eventually depends on the particular demands of the item being created. Recognizing these plastic types can significantly boost the extrusion procedure.
Comparing Plastic Extrusion to Other Plastic Forming Approaches
Recognizing the kinds of plastic ideal for extrusion paves the means for a wider discussion on exactly how plastic extrusion compares to various other plastic creating approaches. These include injection molding, blow molding, and thermoforming. Each approach has its unique uses and benefits. Shot molding, for circumstances, is outstanding for creating intricate parts, while blow molding is perfect for hollow items like bottles. Thermoforming excels at forming superficial or large components. Plastic extrusion is unmatched when it comes to developing continuous profiles, such as gaskets, pipelines, and seals. It also permits for a regular cross-section along the size of the item. Thus, the choice of approach largely relies on the end-product requirements and requirements.
Key Advantages of Plastic Extrusion in Manufacturing
In the world of production, plastic extrusion uses many significant benefits. One noteworthy benefit is the cost-effectiveness of the process, which makes it an economically enticing manufacturing technique. Additionally, this technique gives superior product versatility and enhanced production rate, consequently boosting general manufacturing effectiveness.
Cost-efficient Manufacturing Technique
Plastic extrusion leaps to the center as a cost-efficient production approach in production. Additionally, plastic extrusion needs much less power than typical production approaches, contributing to lower functional expenses. In general, the financial benefits make plastic extrusion a very eye-catching option in the manufacturing sector.
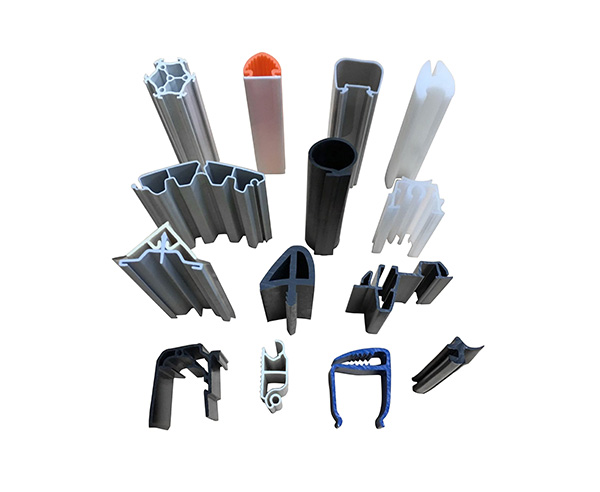
Superior Item Flexibility
Past the cost-effectiveness of plastic extrusion, another considerable benefit in producing lies in its superior product adaptability. This makes plastic extrusion an optimal service for markets that call for tailored plastic parts, such as auto, construction, and packaging. In essence, plastic extrusion's item versatility fosters development while enhancing functional performance.
Enhanced Production Rate
A significant benefit of plastic extrusion depends on its improved production rate. This production process enables high-volume manufacturing in a reasonably brief time period. It is capable of generating long, continual plastic profiles, which substantially decreases the production time. This high-speed manufacturing is especially helpful in markets where big amounts of plastic components are needed within limited due dates. Couple of various other manufacturing processes can match the rate of plastic extrusion. Furthermore, the capability to maintain constant high-speed production without compromising product high quality sets plastic extrusion besides other techniques. The improved production speed, consequently, not only enables producers to satisfy high-demand orders however also adds to increased performance and cost-effectiveness. This advantageous function of plastic extrusion has made it a preferred choice in numerous markets.
Real-world Applications and Impacts of Plastic Extrusion
In the this page realm of look what i found manufacturing, the method of plastic extrusion holds extensive value. This process is extensively used in the production of a selection of products, such as plastic tubing, window frameworks, and weather stripping. Therefore, it greatly affects sectors like construction, product packaging, and automobile industries. In addition, its impact includes everyday products, from plastic bags to toothbrushes and disposable cutlery. The financial advantage of plastic extrusion, mostly its high-volume and cost-effective outcome, has actually transformed manufacturing. Nevertheless, the environmental effect of plastic waste continues to be a worry. Consequently, the sector is constantly making every effort for innovations in recyclable and eco-friendly products, suggesting a future where the benefits of plastic extrusion can be kept without jeopardizing environmental sustainability.
Conclusion
To conclude, plastic extrusion is a very efficient and effective technique of changing raw materials into diverse products. It offers various advantages over other plastic forming methods, including cost-effectiveness, high result, very little waste, and design adaptability. Its impact is profoundly felt in different industries such as construction, vehicle, and durable goods, making it a critical process in today's manufacturing landscape.
Digging much deeper into the technological process of plastic extrusion, it begins with the option of the appropriate plastic material. When cooled, the plastic is cut into the required sizes or injury onto reels if the item is a plastic film or sheet - plastic extrusion. Comparing Plastic Extrusion to Various Other Plastic Forming Techniques
Recognizing the kinds of plastic appropriate for extrusion leads the means for a more web link comprehensive discussion on just how plastic extrusion piles up against other plastic forming techniques. Couple of other production processes can match the rate of plastic extrusion.